One set of 20HL automated brewery system and ready to delivery.
Let’s we see the details of brewery equipment, this is the 20HL this is 3 vessel with mash kettle, lauter tank, kettle whirlpool and extra hot water tank as a combine. 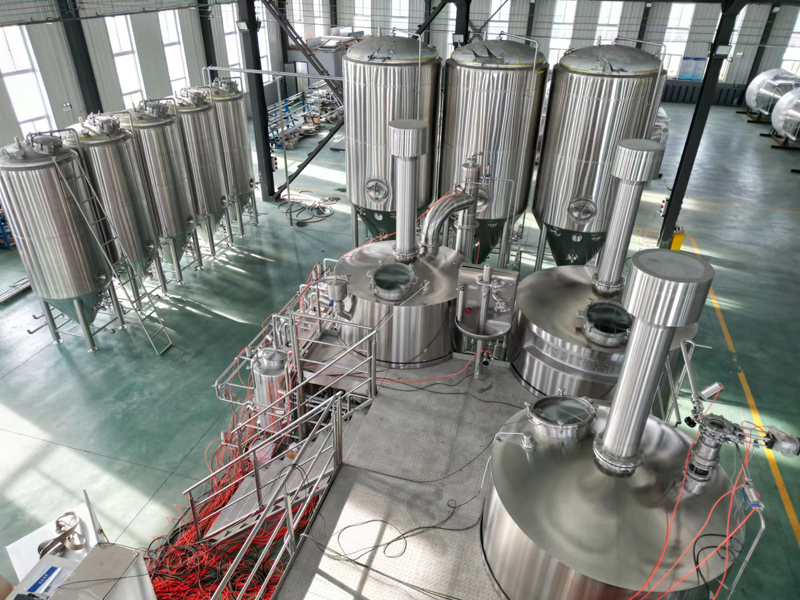
From this brewery set up, First the Brewhouse Highly matched with your brewing request.
The design background is based on plato 12-16 to meet different brewing process and beer. The working volume is 20HL for each vessel, but for total volume is about 3200L, for lauter tank, the diameter is 2000mm, When the wort is 16 plato, the feeding amount is 500KG, the tank volume using for 80%, and grain bed thickness is 340mm, and not more than 350mm, which will effect the filtration speed and brewing efficiency.
Boiling kettle: The kettle volume design is based on the 2320L wort before boiling, and the using volume is 65%. Because of the wort concentration is relative higher in North America, the form will much abundant when boiling. In order to prevent foam overflowing from the kettle during the boiling process, we use the forced circulation function to improve the evaporation rate to ensure the evaporation rate is 8-10% and improve the boiling intensity. A forced circulation with kettle helps increase the evaporation, and the DMS situation and the content within 30PPM, it will reducing the heat loading and ensuring the stability of the wort chroma and avoiding the wort Maillard reaction.
2.Secondly, Lower energy consumption in brewery
1.2.1 Condensate system on kettle: The boiling kettle adopt steam condensation recovery system, it will helps to improve the water recovery and save the water and gas consumption in whole brewery. The recovery hot water temperature around 80-85℃, and hot water recovery capacity at 300L for each batch; That’s means it will save the gas 3m³ per batch of the water temperature from 25-85℃.
1.2.2 Condersate water from jacket: it will a great help to save water and gas in gas steam generator. Only to use less gas to heating it and become steam when the condensed water back to the generator as the condensed water temp is around 80℃.
1.2.3 Wort cooler: The wort heat exchanger area calculate by the brewing process and finish the cooling process in 30 minutes, and hot water temperature at 85℃ after heat exchange, heat exchange efficiency of more than 95%. Therefor, we will ensure the maximum energy recovery and lower production costs.
3.Support Customized to meet different kinds of beer
3.1Hops adding device on kettle and put the dry hops automatic. As we all know North America brewer more like hobby beer and put more hops to adding the taste of hops.
3.2Tubular heat exchanger, To allow the a brewery to cool the wort before adding whirlpool hop additions. There's an external tubular heat exchanger to cool the wort going out and then back into the vessel.
4.Fully automatic brewhouse
A commercial automated brewing system is a technologically advanced solution designed to simplify and optimize the brewing process on a commercial scale. The brewing system will combine the work with the pneumatic valve, the automatic regulating valve and level switch to achieve automatic operation of water inlet, feeding, temperature, etc., thereby improving the brewing efficiency and save labor in brewery.
The automation of these functions not only ensures a higher quality of beer but also allows breweries to operate more efficiently, reducing wastage, and increasing profitability.
For mash kettle,
1.1 The point is pre-masher, the system increases yields, shortens mashing work and leads to a lower iodine index. The dynamic mixing system prevents the accumulation of grist and reduces the energy requirements for mixing. Thus, the husks are protected and the mashing times are significantly shorter. The entire mashing process can be observed through the aesthetic sight glass. The unit is completely CIP compatible.
1.2 Agitator is a flow-optimized mixing system with a specific circulation flow throughout the complete volume of mash, even at low speeds. This defined flow pattern ensures a uniform temperature distribution in the mash, increased yields and protected husks.
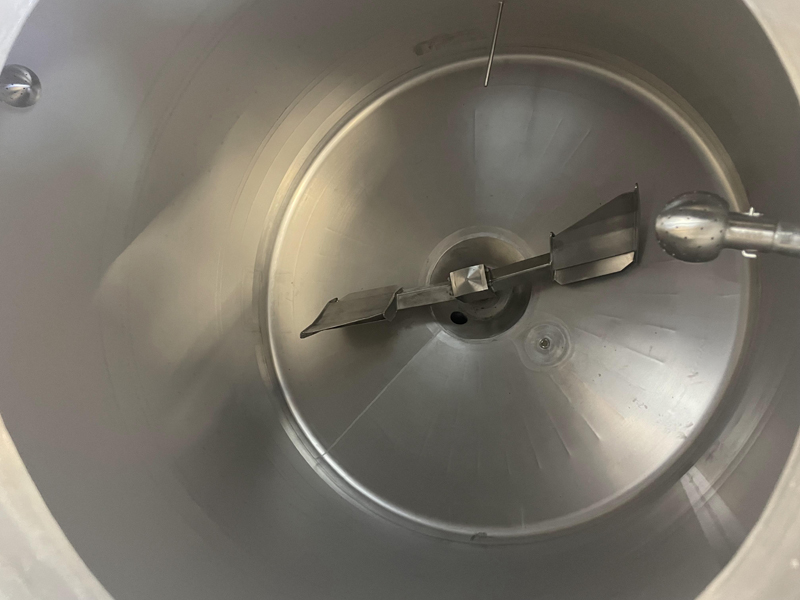
For lauter tank,
1.1 Raker system is automatic lift and spent the grain automatic too. Flexible grist load heights and miminum set-up times, our system allows for a flexible grist load height: Perfect lautering is ensured not only with extremely high grist loads, but also with very low grist loads for light beers. This makes the system an ideal tool for the brewing of craft beer. In general, our system achieves setup times of under 10-20 minutes for spent grains removal and flushing the system, including filling the false bottom. This is made possible by the improved drive technology of the spent grains removal mechanism and through the efficient, water-saving flushing of the false bottom.
1.2 Sparaging system is much closer to grain bed and not broken that for less oxygen and not effect the filtering.
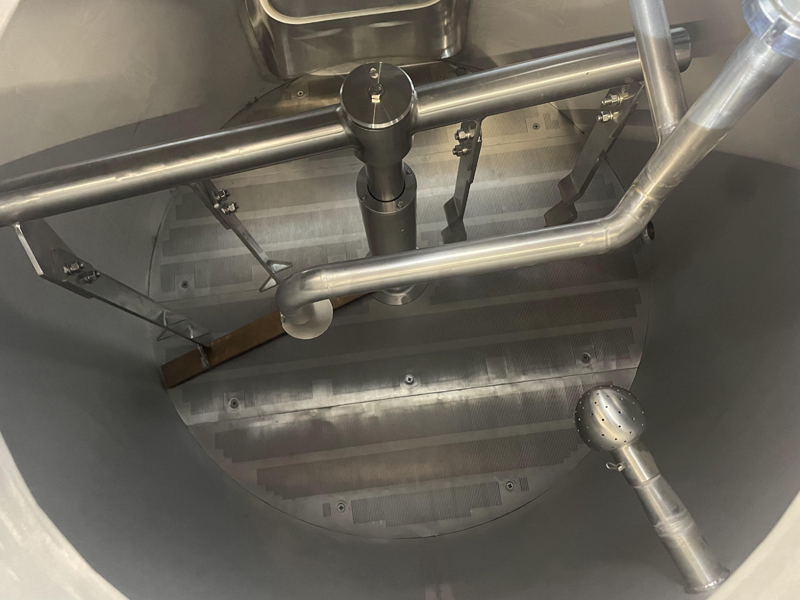
1.3 Long probe for precisely temp transmission, double cleaning ball both cleaning the vessel and glass manhole, the ladder to help you to check inside, the Protection net for brewer safety, Visual lamp is explosion -proof, the temp sensor and level switch attached connect to Industrial cabinet to achieve the automatic version.
For Water station, we use Pneumatic valve, regulation valve, temp testing, level flow meter to automatic adjust the water temp, flow and water volume through the control panel.
For steam line, all connection is flange to prevent the steam leak and loose after long term running. Also there is a valve for here installed to back flow of condensate and Preventing water hammer in the pipes.
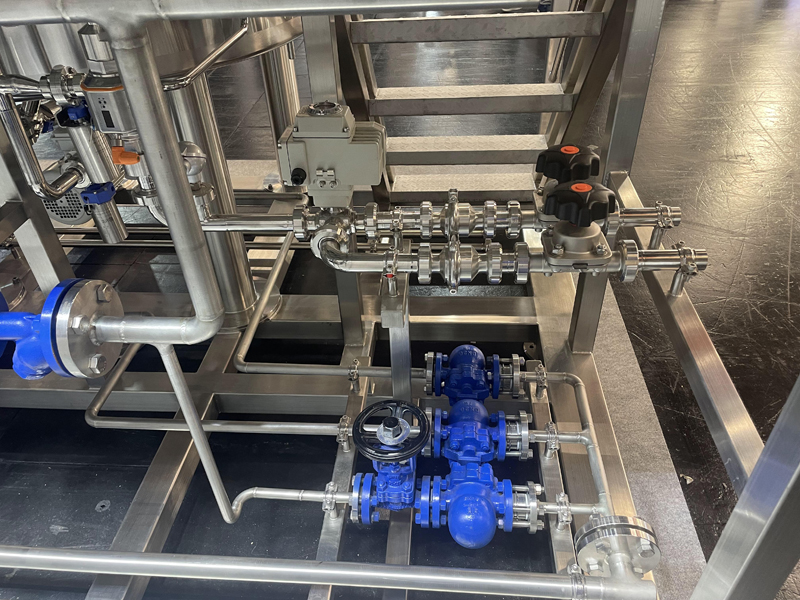