The main way of beer filtration - diatomite filter
For beer filtration, the most commonly used filtration equipment is diatomite filter, cardboard filter and sterile membrane filter.
The diatomite filter is used as the coarse filter of beer, the cardboard filter is used as the fine filter of beer, and the sterile membrane filter is mainly used to produce pure draft beer.
In modern beer enterprises, there are many types of diatomite filters, among which the plate-and-frame type, candle type, and horizontal disc type are the most common.
1. Plate and frame diatomite filter
The plate and frame diatomite filter is composed of a frame and filter frames and filter plates suspended on it alternately, and the material is mostly stainless steel.
Support plates are hung on both sides of the filter plate, and the filter frame and the filter plate are sealed to each other. The support board is made of fiber and condensed resin.

2. Candle type diatomite filter
(1) candle wick
The filter candle wick is a filter material, and the filter aid diatomaceous earth is pre-coated on the candle wick.
For filtering, the helix is wound around the candle wick in the radial direction, and the distance between the wires is 50~80m.
The filter wick can be as long as 2m or more. Since nearly 700 candle wicks are installed in the filter, the filter area formed is very large, the filter efficiency is very high, and there are no moving parts on the candle wick.
(2) Working process
The main body of the candle type diatomite filter is a vertical pressure tank with an upper column and a lower cone.
There is a candle wick bottom plate under the machine cover of this type of filter, on which the suspended candle wick is fixed, and a series of auxiliary equipment such as pipelines, connectors and testing instruments are equipped.
Care should be taken with these ancillary equipment to ensure minimal oxygen uptake during and after filtration.
A. Fill the filter
B. Precoat
C. cycle
D. Start filtering
E. Beer Filtration
F. Filtration ends
G. Discharge
H. cleaning
I. Sterilization
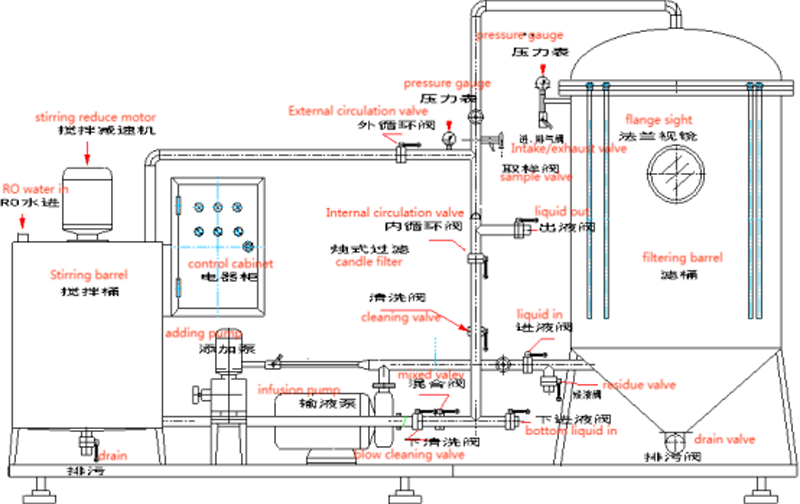
3. Horizontal disc diatomite filter
The horizontal disc type diatomite filter is also called the blade filter. In the filter, there is a hollow shaft, and multiple discs (filter units) are fixed on the hollow shaft, and the discs are used for filtering.
From the cross-sectional view of the horizontal disc diatomite filter, the filter disc can be clearly seen, and the structure of the horizontal filter disc is also varied. In the horizontal disc type diatomite filter,
the filter support material is a filter disc woven with chrome-nickel steel material, and the pore size of the metal screen is 50-80 μm.
In this filter, only one layer of metal mesh is fixed on the upper surface of the horizontal disc. It is evident that diatomaceous earth adheres well to the horizontal discs.
It works on the same principle as a candle diatomaceous earth filter . The added diatomaceous earth is evenly distributed on each disc, thus forming a uniform filter layer.
The muddy waste diatomaceous earth can be discharged by the centrifugal force generated by the rotating filter disc. There are usually several different rotational speeds to choose from.
When cleaning, the rotation speed of the filter disc is very slow, and the disc is strongly washed while rotating.
Since the diatomite filter is very popular in breweries, we will focus on its operation process.
When filtering with a diatomite filter, filter aids such as diatomaceous earth or perlite are coated on the filter support material.
Since the continuously added filter aid particles are very small and cannot be retained by the filter material, pre-coating is necessary.
Filtration can only be performed after the pre-coating is completed. During the filtration process, the filter aid should be continuously added until the filtration is completed.
As the filtration progresses, the filter layer becomes thicker and thicker, the pressure difference between the inlet and outlet of the filter becomes larger and larger, and its filtration capacity becomes smaller and smaller until the final filtration ends.
1. Precoat
(1) The first pre-coat
(2) Second pre-coat
(3) Continuous feeding
2. Treatment of the head and tail of the wine
3. Dosing of diatomaceous earth
Problems prone to occur in diatomaceous earth filtration operation
(1) The failure during filtration often occurs in the process of emptying after pre-coating, and the filter layer is sometimes damaged
(2) The amount of diatomite added was too low, and the yeast could not mix with diatomaceous earth to form an additional support layer. This part of the yeast forms an insulating layer that, over time, causes the pressure to grow too quickly.
(3) Yeast shock generated during filtration comes from large yeast agglomerates, which form slight or severe blockage in the filter layer. The severity of yeast clogging can be shown on the curve of differential pressure change.
(4) If the amount of diatomite added is too high, the filtration curve will be too flat, and the filter cavity will be filled with diatomite in advance, resulting in difficulty in filtration.
If you are planning to open a brewery. Alston Brew team could help you answer your questions and supply the brewery equipment system.
We supply 2-150bbl complete beer brewing brewery equipment system including malt milling equipment, brewhouse equipment, fermenters, brite beer tanks, beer bottling machine,beer canning machine, beer kegging machine, hopping machine, yeast propagation equipment.
We also supply all auxiliary brewery systems like steam heating pipe and valves, water treatment, filter, air compressor etc. Everything in brewery are all in our list.